How Software Streamlines Packaging Development for Improved Efficiency Across the Board
7 min read
Topic:
ASP.NET Development Services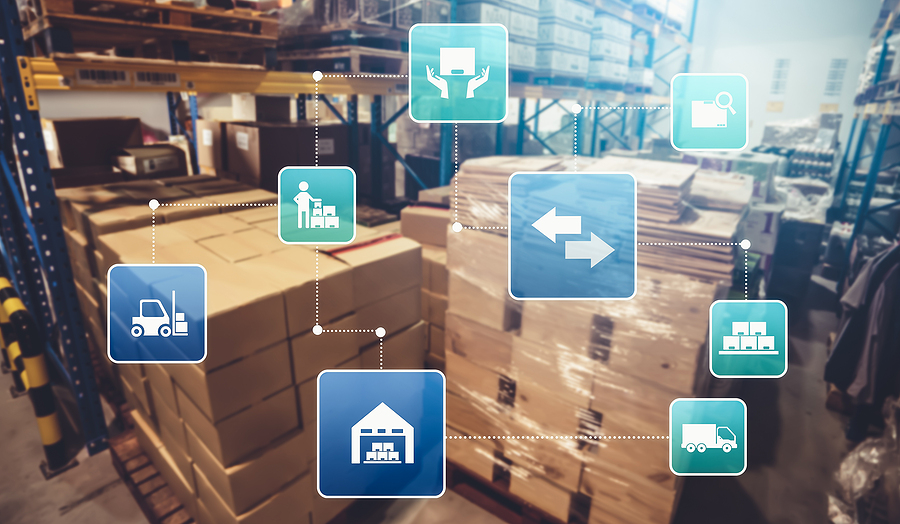
Regardless of the type of business you're running or even the industry that you're operating in, every manufacturer has a basic need for packaging that safely encloses their products for shipping to contain things as effectively as possible.
Not only does this help make sure that customers are able to enjoy the experience that you've designed for them, but it also helps to prevent damage in transit - among other issues.
According to one recent study, the worldwide packaging industry is expected to hit an enormous $1 trillion in value by as soon as 2024 - underlining just how important this topic has truly become.
Yet at the same time, designing and producing product packaging takes a great deal of time, care and attention - all of which takes the focus of professionals away from equally important tasks. Therefore, the process to manage the development of that product packaging is an extensive one - meaning that manufacturers are looking for ways to automate the process in any way that they can.
Development of Packaging
Every new product that is designed by a product team has to be packaged without exception. Those packaging engineers will come up with several specifications for all components necessary based on the precise products that they're working with.
If you're trying to safely and securely ship a beverage, for example, there are a number of different elements at play. You'll need a bottle design, a cap design, a design for the label artwork - the list goes on and on. Equally important will be a corrugated box design to make sure that everything can move through the supply chain securely. You'll also need a label on the box, as well as separators within that box to keep the bottles from smashing into one another. Lastly, a pallet pattern design will be necessary to show how those boxes will be stacked on a pallet.
The point is that product packaging is almost as important as the product itself - and it takes a significant amount of time and effort to "get this one right."
All of this design information will be comprised from a wide range of different sources, including but not limited to Microsoft Word documents, CAD drawings, label artwork that will likely be created as Photoshop files and more. Also included will be quality assurance documents and specific packaging instructions to make sure everyone involved is always on the same page. Packaging document control becomes an uphill battle on the best of days, especially if you have hundreds of products in your product line.
A bill of materials will also be produced at this point, which will include a detailed outline of everything involved in the package itself. More often than not, the marketing team will be heavily involved in coming up with a plan for packaging and those packaging specifications will need to be signed off on by other departments. Everyone will have a hand in the proceedings: the manufacturers themselves, the packaging department, quality assurance, management, the legal and/or regulatory departments and more. A delay in any one department can lead to delays in getting a new product to market.
Naturally, this is very much one of those situations where there could be "too many cooks in the kitchen," so to speak. If there is a delay at the quality assurance stage, it only extends the amount of time that it will take to get things through the legal process and beyond. This again stands to harm not only the quality of the products themselves, but the experience that a brand is trying to create for its customers.
In a perfect world, a web-based packaging development software system would be employed to not only capture all of this information but to distribute it - all while tracking the workflow of getting approvals for maximum efficiency, no matter what.
How Packaging Paperwork Bottlenecks Hurt Revenue
It is common that when a new product is being developed, especially in those industries that are highly regulated, the creation of packaging and all related content requires approvals from many stakeholders for regulatory reasons. While this is an important part of the process, it isn't necessarily the fastest one - something that could cause issues for all the reasons outlined above.
When an organization is still using traditional techniques, this approval process can take months - something that is problematic, especially if you're trying to build anticipation for an upcoming product launch.
By using a software-based solution to manage the packaging information and approval, on the other hand, this process can be done not in months or weeks, but in days. This enables the company to sell the product faster, thus generating a significantly larger amount of revenue than they would otherwise be able to.
Examples of How Custom Web-Based Software Solutions Have Helped Companies Package Their Products
There are a number of clear-cut examples of how custom web-based software solutions have helped companies package their products - and the team at McCormick is chief among them.
As an international producer of spices, seasonings, flavorings and specialty foods, McCormick has an understandably broad product line with a reach that touches both the retail and industrial markets. On the retail side of the business, packaging specifications are the product of the package engineering department. In the industrial division, however, these same responsibilities are typically handled by either purchasing, quality assurance or the manufacturers themselves.
In the past, product specifications were written out in a standard word processor and were distributed via an internal mail system. This was problematic considering that sometimes 100 or more changes per day could be made in the retail division alone. After partnering with Keene Systems, a custom solution was developed that easily managed all of this information via a single application - including but not limited to CAD drawings, graphics, supporting text documents and more. Not only did this decrease the significant time lag that had become a staple of the process, but it dramatically increased efficiency as well.
Another great example of how these types of custom solutions have benefited organizations takes the form of Janssen, which itself is a division of Johnson & Johnson. Here, packaging allowed them to manage significant growth in their products in a number of interesting ways.
Janssen manufactures pharmaceutical drugs with multiple locations around the world. During one period of their growth history, it increased the number of products in its line from eight to 30 - which of course resulted in an increase from about 250 packaging documents to more than 1,600 over the same period of time.
As Janssen began to scale its business, it became clear that their existing manual specification management process wasn't capable of keeping up. Officials needed a way to get documentation into the hands of the people who needed it to do their jobs - and that simply wasn't possible under the old system.
Janssen partnered with Keene Systems to develop a custom solution to prevent a lot of the issues they were experiencing - from data getting routed to the wrong person to critical documents being misplaced entirely. Once data was entered into the specification system, all important elements and other material specification information was made available over the network instantly to the appropriate team members - something that allowed Janssen to handle a six-fold increase in specifications information without adding a small army of additional staff members in the process.
Hormel Foods is also an example of a team who has benefited from this approach, as it allowed them to manage product expansion and packaging regulations in a more effective way. Prior to converting to a more modern, computerized system, the team at Hormel Foods was still using a paper-based "routing form" to accomplish the admittedly complicated packaging redesign approval process. A product manager on the marketing side of the business would initiate a design request for a package, for example. Then, that request would need to be moved through six or more parties in the design phase alone - something that lived in each department until the necessary action was taken and approval was granted.
Needless to say, this took a tremendous amount of time. Each person in this process would usually sign off on every label at least two times - once in a rough format and again once art had been finalized. When you begin to consider how many parties were involved in Hormel Foods' then 20 production facilities across the United States, you begin to get an idea of just how time-consuming this really was.
At the same time, new federal labeling regulations were being developed - meaning that constant changes to product packaging became a way of life. In an effort to help streamline things as much as possible, Hormel turned to a custom packaging specification software system from Keene Systems. Immediately after deployment, it became possible to present proposed changes to multiple users simultaneously - all in a way that also helped manage the company's custom workflow as well. The use of this software alone helped the company reduce its typical approval time for changes from three weeks all the way down to seven days. In certain situations that don't require submission to government agencies, those approval times have been reduced all the way down to 48 hours or less.
Finally, we arrive at Monsanto - an organization that was able to cut time for packaging approvals by 97% in some cases simply by employing custom packaging management software in a more strategic way.
While the Monsanto Agricultural Group was using a company-generated database - complete with a hard copy backup - for packaging design and approval, it too ran into an issue as it continued to scale. Officials had to coordinate 500 different packaging SKUs across 15 locations spread all over the globe - a tall order, to be sure.
At the beginning of the process, Monsanto's packaging approval process involved 12 steps that had to be completed in a specific order. Documents would need to make their way not only around the company's headquarters, but also to plant facilities and more. If a delay happened at any one of these steps, it could extend the process by weeks. If a package designer wanted to get an update on the progress of the approval, this was also difficult to track because information was spread in so many places.
This also created the added issue where plant managers didn't know which packaging components should be prioritized - leading to packages that were no longer used or that were created in the wrong size.
Thankfully, the installation of a new custom packaging software solution helped to relieve all of these issues and more. After implementation, Monsanto's packaging approval process no longer took two or three months - it was reduced to two or three days.
Packaging Quality Control
In the end, it's important to understand that manufacturers from virtually every industry have the need to manage their product packaging process in a more effective way than ever before to ensure quality and consistency. In many industries, there are also significant regulations on what must appear on the packaging itself - a process that also needs as much visibility as possible.
Every company will have its own unique process for developing its products - indeed, this is what forms the basis of their critical competitive advantage in their industry. These custom software systems should always include package management software that is web-based to enable their teams to manage the package development process that, along with the approval and manufacturing processes, will allow them to maintain speed, quality and consistency in equal measure.
Off-the-shelf systems are a one-size-fits-all solution in a context where the opposite is needed. You can't create a competitive advantage if you're still being forced to contend with the tools that everyone else is using. Instead, you need something that will play to the strengths that make you unique and successful to begin with - something that only custom software will do.
The best custom packaging management solutions are built using tools like Microsoft ASP.NET and SQL Server - both of which are the best way to create an enterprise-class product that is scalable for any manufacturer. Being web-based allows packaging specification information to be routed to the correct team member at any time, anywhere, over the internet, even via mobile phones. This is something that has only become more important in the last decade, especially during the COVID-19 pandemic and it's a trend that shows no signs of slowing down anytime soon.
To find out more information about our ASP.NET software development outsourcing capabilities, or if you’d like to discuss how software streamlines packaging development with Keene Systems CEO, Lance Keene click here to book a call with him. You can also download our eBook - Why ASP.NET Development Services Fuels Business Growth - to learn more about this essential topic.